Pollution is 100% about Health; the health of both people and planet. For this reason, we will measure the damage pollution is doing to people by imposing a ‘Health Tax’ on it, which will aid us in paying for our new affordable and Universal Health care. We will solve the damage pollution is doing to the planet by taking control of the businesses that are inflicting this harm.
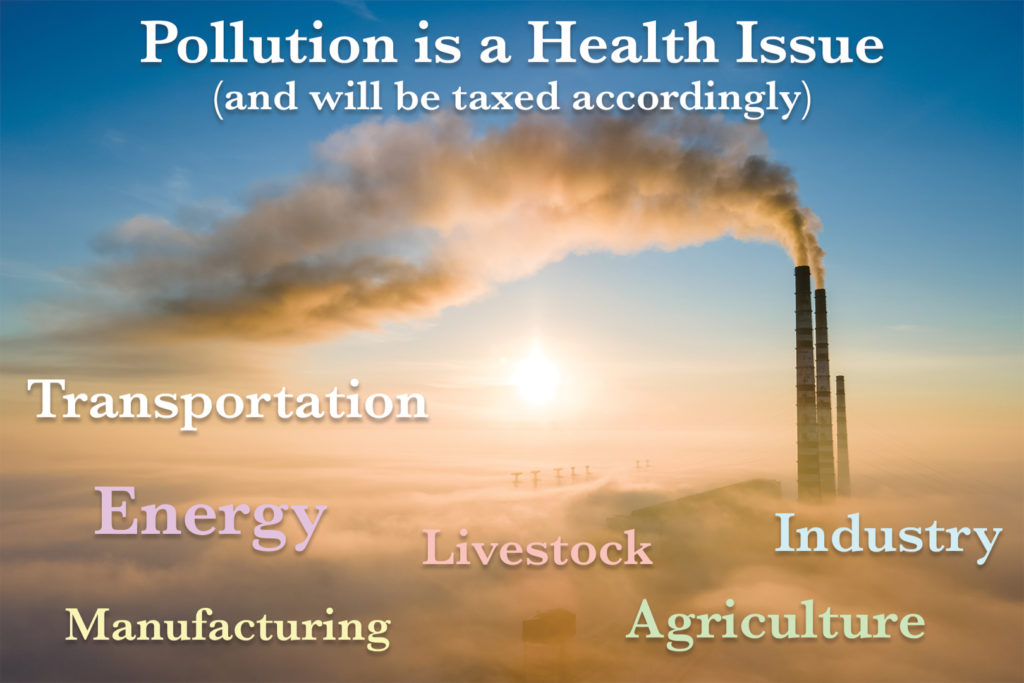
I. Health Taxes for Pollution
The overall Carbon Tax rate will be $37 per Metric Ton of Carbon produced [some experts argue it should be $220-230 per MT, so be happy we settled on this figure. This will lead to the following costs to consumers:
Gasoline Tax Proposal:
- 32.9 cent tax per gallon on gasoline = $40.63 Billion
- 37.6 cents per gallon on diesel = $16.7 Billion
- 35.4 cents per gallon on Jet Fuel = $6.124 Billion
Electricity Pollution Tax Proposal:
- 1.7 cents per KwH of electricity used
NOTE: the consumer has no control over electric company’s choice of electricity generation, but between coal and oil and natural gas, 1823.08 MMT of Carbon is being produced. We will spread the cost out among everyone.
Mercury Emissions Tax Proposal:
- Mercury Emissions Tax of 2.2 cents per pound on any coal used or purchased
NOTE: The mercury released by coal-fired power plant is converted into a far more toxic form when it enters the food chain. We will use the current calculation of 665 million short tons of coal burned / year [1.33 trillion pounds] and the $29 billion in direct Health Costs it produces.
Other Energy Sources Tax Proposals:
Coal tax = 4.8 cents per pound (typical 25 lb bag = $1.20 tax)
Heating Oil tax = 37.6 cents per Gallon
Wood Burning tax = 3.2 cents per pound of wood (a cord of wood could run $126.92 in taxes)
Charcoal Tax = 0.5 cents per pound
Propane, Kerosene, Gas Water Heater., gasoline-powered boats = one cent per gallon
Spray paint, solvents, degreasers, and paint removers = 2 cent per gallon
Agriculture Tax Proposals:
- $34.26 per acre Land Use (Carbon) Tax on Agriculture*
*In theory, planting trees or pasture or fertile grassland actually captures carbon instead of emitting it – every acre of agriculture land that is used in this manner will not be charged
- 20 cents per pound added to beef
- 5 cents per pound added to pork, veal, lamb, and mutton
- 4 cents per pound added to chicken and turkey
- Meat causes $2 Billion in water pollution = 2.1 cents per pound tax added to all meat
SOURCES:
- 44.4% of the emissions come from the Agriculture Soil [decaying of organic soil releases CO2, methane, and nitrous oxide] or 260.2 million MT = $9.627 Billion. Breakdown:
- 216 million acres of land used for livestock
- 62 million acres used for wheat
- 3 million acres for vegetables
NOTE: Not all ground can grow food. Because soil is not organically rich in nutrients, it needs to be treated in order to sustain crops, resulting in GHG Emissions.
- 57% of GHG Emissions are related to synthetic fertilizer
- 36% is related to use of lime to improve soil quality, make it more alkaline
- 13% related to residue crops laying around viable)]
- 37.8% more comes from the Livestock [but beef requires 28 times more land, 6 times more fertilizer and 11 times more water than producing pork or chicken – this means that “producing beef releases four times more greenhouse gases than a calorie-equivalent amount of pork, and five times as much as an equivalent amount of poultry.” [If chicken is a “1”, then pork = ‘1.25’ and beef = a “5”]
- Also, within Agri-business, CO2 is released during fertilizer manufacture, and during refrigeration
- Animals make 100-164 times the waste that humans do, but it is often not regulated – Industrial agriculture is among the leading causes of water pollution in the United States. The Environmental Protection Agency (EPA) determined agricultural activity was identified as a source of pollution for 48% of stream and river water / 41% of lake water.
NOTE: From the EPA – Unless prohibited by other State or local laws, agricultural producers can dispose of solid, non-hazardous agricultural wastes on their own property. This includes:
• manure and crop residues returned to the soil as fertilizers or soil conditioners, and
- solid or dissolved materials in irrigation return flows.
TAKEAWAYS
- We all need to eat less meat – by charging the actual price for meat, consumers will be better able to understand the unsustainable nature of it.
- People don’t really need soybeans and the corn that much —instead, we should plant pastures and trees and even add fertile grasslands and we won’t charge Agri-business owners the land use tax.
IT IS IMPORTANT TO ATTACK BOTH SIDES OF THE PROBLEM
Plains used to hold tall grass, more trees, that created a huge carbon sink – we need to capture / sequester carbon at the same time we are reducing the production of it. “Supply-side approaches, centered on CO2 sources, amount to reshuffling the Titanic deck chairs if we overlook demand-side solutions: where that carbon can and should go,” says Thomas J. Goreau, a biogeochemist and expert on carbon and nitrogen cycles who now serves as president of the Global Coral Reef Alliance. Goreau says we need to seek opportunities to increase soil carbon in all ecosystems — from tropical forests to pasture to wetlands — by replanting degraded areas, increased mulching of biomass instead of burning, large-scale use of biochar, improved pasture management, effective erosion control, and restoration of mangroves, salt marshes, and sea grasses.
All Greenhouse Gas emissions:
- Carbon = 82%
- Methane (CH4) = 10% (cows, natural gas)
- Nitrous Oxide (N2O) = 6%
- Fluorinated Gases = 3%
- IMPORTANT: fires release about 290 million metric tons of carbon dioxide a year
BOTTOM LINE: Meat will not survive the way it is currently produced, with taxes on water and pollution and land value. Providing Anaerobic Methane Digesters to farms can capture farm waste, and turn it into electricity, potable water, and more fertilizer for the soil. Money for these “Omni-processors” can come from the water pollution tax, and could help eliminate this tax in the future.
Omni-Processor Facts
‘Anaerobic Methane Digesters’ can capture 18.25 metric tons of CO2 per ton of methane per year, by placing farm waste such as manure into an airtight chamber which then harnesses emitted gasses and converts them to energy that can be used to power nearby appliances, electronics, and even homes. The remains can also be used as excellent sources of fertilizer. Alberta-based Livestock Water Recycling has machinery already processing manure into commercial-grade fertilizer, then distills the water for irrigation and farm animals. Today, the company has systems (which cost up to $1.5 million to install) in New York, Michigan, Wisconsin and Indiana.
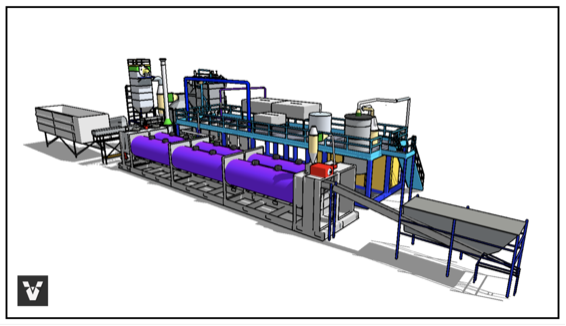
Human Waste Management
The Third Option wants to place the next generation of Omni-Processors in every Community, to handle the waste from 100,000 people, in order to produce 86,000 liters of potable water per day and generate a net 250 kw of electricity.
II. Taking Control of Pollution-Causing Businesses
Because of the polluting nature of U.S. Energy Production, and its effect on every area of the economy (industrial, residential, agricultural, et al), the problem of pollution cannot be solved until we take complete control of our Energy Grid. Similarly, We must also get control of Agriculture and Transportation, which each pose their own specific pollution problems. The National Bank can seamlessly transition us into ownership and management positions in these areas of the economy, where we can promote more eco-friendly infrastructure choices.
Some specific businesses will also need to be funded through the Bank, in order to better control their waste management. We break down two such categories below: Construction and Transport.
In Construction
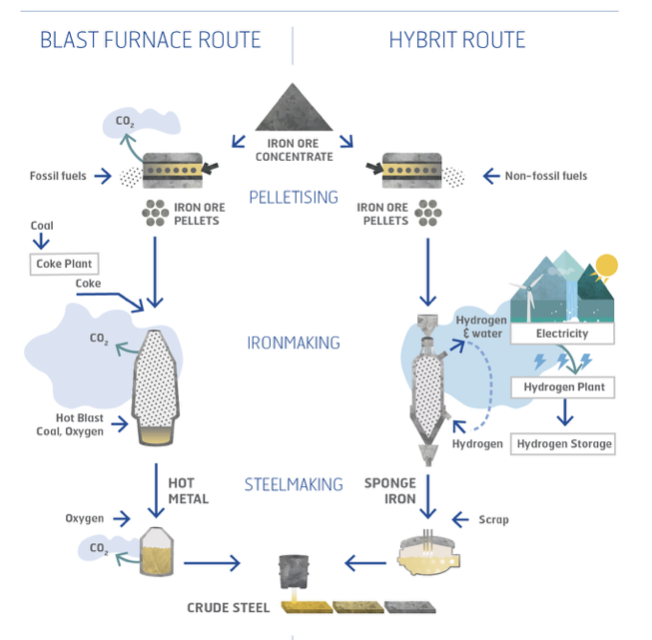
Steel
Experimental ‘Zero Emission’ Integrated Steel Business, and Recycled (Mini) Steel Businesses:
Steel currently has a 68.5% share of the multi-storey offices market, and a 65.0% share in multi-story retail, education, leisure and health care. Takeaway: We need a lot of Steel. And the price of scrap steel is going up, as the supply quickly diminishes.
Business Model
The goal is to produce new “zero carbon” steel; to make our Integrated Steel Mill We will need a $10 Billion Bank Loan (Engineer Les McLean puts the price tag for an Integrated Steel Mill at $5 Billion, although Ours will be using Hydrogen and not Carbon Dioxide in the iron reduction process, which costs more, thus the $10 Billion estimate, although We hope to corner the Hydrogen market with Our Waste Management Business). To pay back this loan will cost us a monthly payment of $47.74 Million [or $572.9 Million a year] and yield $17.2 Billion in 30 years. How will We pay this $572.9 Million a year mortgage cost?
We will sell off all the “non-ferrous” metals We collect from the Salvage Yards where Our 10 Mini-Mills are recycling scrap metals. Some non-ferrous metals will also be extracted during the Iron Ore mining process.
Statistics show that non-ferrous metals are only 11.9% of all current metals recycled (67 million metric tons of steel and iron versus only 8 million metric tons of aluminum, copper and the like), yet non-ferrous metals pay 63.6% of the dividends ($18.2 Billion made from ferrous metal sales versus $32 billion for non-ferrous metals).
Our goal will be to make 3.6 million tons of steel in a year, which could mean We will also have 428,000 tons of non-ferrous metals, potentially worth over $5 Billion; this is certainly more than the $572.9 Million We will need in order to pay the mortgage on this Loan.
NOTE: the carbon tax we impose on private steel could perhaps also help fund the building of our Integrated Plant if necessary. If so, We will make sure to share any technology discoveries, so this carbon tax can end up benefitting the private steel business rather than penalizing it.
CONCLUSIONS ABOUT HYDROGEN IN STEEL MAKING [from M. KUNDAK et al.: CO2 EMISSIONS IN THE STEEL INDUSTRY]
- Most of the CO2 generated by today’s steel industry comes from the chemical interaction between carbon and iron ore in blast furnaces. This process, known as iron reduction, produces molten iron which is converted to steel.
- Substantial further reductions in CO2 emissions will not be feasible if only conventional technologies are used.
- A major reduction in CO2 emissions in today’s steel production can be achieved by use of electric arc furnaces as well as by direct ore reduction using hydrogen. An increase in steel production by means of an electric process requires cheaper electric energy, which, in the future, might be achievable either from alternative energy sources or from nuclear energy. The price of pellets or briquettes from the ore reduced by hydrogen is currently relatively high because of the high cost of hydrogen as reductant. In the next 30 years, the cost of hydrogen production is expected to fall, but it will still be higher than the ore reduction by carbon. Therefore, in the near future, steel production is still expected to rely largely on the reduction by carbon.
HISTORY:
US Steel operates a number of integrated steel mills, including the Gary Works in Gary, Indiana. They also operate the Edgar Thomson Works, which is the iron- and steel-making unit of the Mon Valley Works, which includes three other related plants. The Company operates the Great Lakes Works, and Granite City Works. ArcelorMittal operates three integrated steel mills: in East Chicago, Indiana, Burns Harbor, Indiana, and Cleveland, Ohio.
AK Steel Corporation has three integrated steel mills, one in Middletown, Ohio, Dearborn, Michigan and the other in Ashland, Kentucky. At present, the Ashland Works is temporarily idled.
In 2014, the United States was the world’s third-largest producer of raw steel (after China and Japan), and the sixth-largest producer of pig iron. The industry produced 29 million metric tons of pig iron and 88 million tons of steel. Most iron and steel in the United States is now made from iron and steel scrap, rather than iron ore. The United States is also a major importer of iron and steel, as well as iron and steel products.
As of 2014, 149,000 Americans were employed in iron and steel mills, and 69,000 in foundries. The value of iron and steel produced in 2014 was $113 billion.
As of 2015, major steel-makers in the United States included: ArcelorMittal USA, AK Steel, Carpenter Technology, Commercial Metals Company, Nucor, Steel Dynamics, and U.S. Steel.
Recycled (Mini) Steel Businesses
BUSINESS PLAN
We will need:
- 10 Operating Mini-Mills Built on Federal Land near Rail Lines that can Recycle 400,000 tons per Mill per year
- A Ferrous and Non-Ferrous Metal Recycling Yard
- Shredding Plant – complete, state-of-the-art 60 x 90 shredding plant [installed] for roughly $4.1 million (need a football sized space to fit it)
- Build all three next to each other, right next to Our Transportation Rails
$260 Million per Operation X 10 locations = $2.6 Billion Loan (will yield $4,468,607,000 in 30 years) Monthly Mortgage = $12.4 Million, or $149 Million a year.
Again, the hope is that this amount will be absorbed into Housing Loan, or covered through the sale of all non-ferrous metals We collect – worst case scenario, We add $2 a month to everybody’s rent.
STRATEGY
- Mini Mills will recycle already-made steel (steel is like glass, very easy to keep re-using) – We may need to offer people more than $150 per ton for their automobile to get them to give it to us. We need a junk yard / salvage yard, recycling plant, and a mini mill all in one place, perhaps right next to Our rail lines in order to transport and receive Our products.
- In the past, China has purchased some of our scrap metals – now we will need to keep all of it – this may make someone happy – China supposedly suspended imports of recycled goods during tariff wars in mid 2018 – maybe we can get recycled steel cheaply from our own people – whoever wants to give us a good price will profit, those who don’t may be driven out of business if they are not careful
- Another thought: If we can invent new electric transportation in a timely manner, we may be able to entice “trade in’s” of old vehicles for our new “Pod Cars”, and get the recycled steel without giving up any actual cash for it. BOTTOM LINE: Please give your scrap metal to Us, as it will put money in your pocket and help Our fellow citizens.
- Best guess is that a steel framed house of 4000 sf needs 8800 pound of steel in it, or 4.4 tons (in reality we just need the support beams). Mini-Mills can produce 200,000 tons up to 3 million tons of steel in a year. For our Affordable Housing alone, we might need our Mills to make 4.4 (tons) X 3.27 Million (houses) divided by 4 (years) = 3.6 million tons of steel a year. If our Mill produced 400,000 tons per year, we would need 9 Mills. Let’s round it to 10. [If these number are not reasonable or feasible, We overall have 8 years to achieve this, perhaps 2 years to set it up and 6 years to produce the steel, if that helps]
HELP WANTED
- Cost of labor for our plants / mills, plus any material cost, is not yet figured into the equation. We know the drill now, the smart people will figure it all out. All We are trying to do is get the steel as cheaply as We can for the Infrastructure We need.
- There is no need to produce steel faster than we can use it – again, the smart people can figure out if we only need 5 Mills, or 3, or maybe we need all 10 because of many of Our other Infrastructure Projects also need lots of steel, too.
RECYCLING IS GOOD
A reduction in energy consumption as well as in the use of other materials. For example, recycled aluminum requires 95 percent less energy, while copper needs 90 percent less, and steel 56 percent less. Additionally, the recycling of one ton of steel avoids the use of 2,500 pounds of iron ore, 1,400 pounds of coal and 120 pounds of limestone.
In terms of volume, ISRI estimated that the United States recycled 67 million metric tons of ferrous metal was recycled in the U.S in 2015. The largest source was provided by the 11 million automobiles which were recycled. The average car contains 2,400 pounds of steel and 300 pounds of aluminum. Auto recycling is the 16th largest industry in the U.S. and generates about $25 million in annual revenue. There are currently about 7,000 auto recycling businesses throughout the U.S. Each year, automobile recycling yields enough steel to produce nearly 13 million new vehicles.
Recycling rates for metal are generally high, due to its value. For example, ferrous metals have a recovery rate as follows:
- for cars: 106 percent
- for appliances: 90 percent
- for steel cans: 66.8 percent
- for structural steel: 98 percent
- for reinforcement steel: 70 percent
NOTES:
Two types of steel used in construction: cold rolled light gauge and hot rolled structural beams. Both types are impervious to rot and insects while being nearly fireproof. Steel is flexible, durable, and long-lasting; it doesn’t swell, warp or shrink. Water is the only real threat, so steel is galvanized with zinc and /or aluminum to fight rust.
Hot Rolled Steel Beams – $15 to $75 per linear foot for materials.
- Ranges depend on the thickness and width.
- Types include I-Beams, H-Beams and S-Beams.
- Both high and low-rise buildings and multistory homes use structural beams to carry the additional load of the multiple stories. The more stories, the more need for structural steel, though its almost always used in combination with light gauge steel.
Light Gauge Cold Rolled Steel – $0.50 to $1.50 per linear foot for materials.
- Most residential projects use this type of framing with limited beams for carrying loads in large open concept and multistory homes.
- Thicker cold rolled steel—16 and 18 gauges— is used for load-bearing walls.
- Can typically support one floor and the roof. Any more stories and structural engineers begin including structural steel for added support.
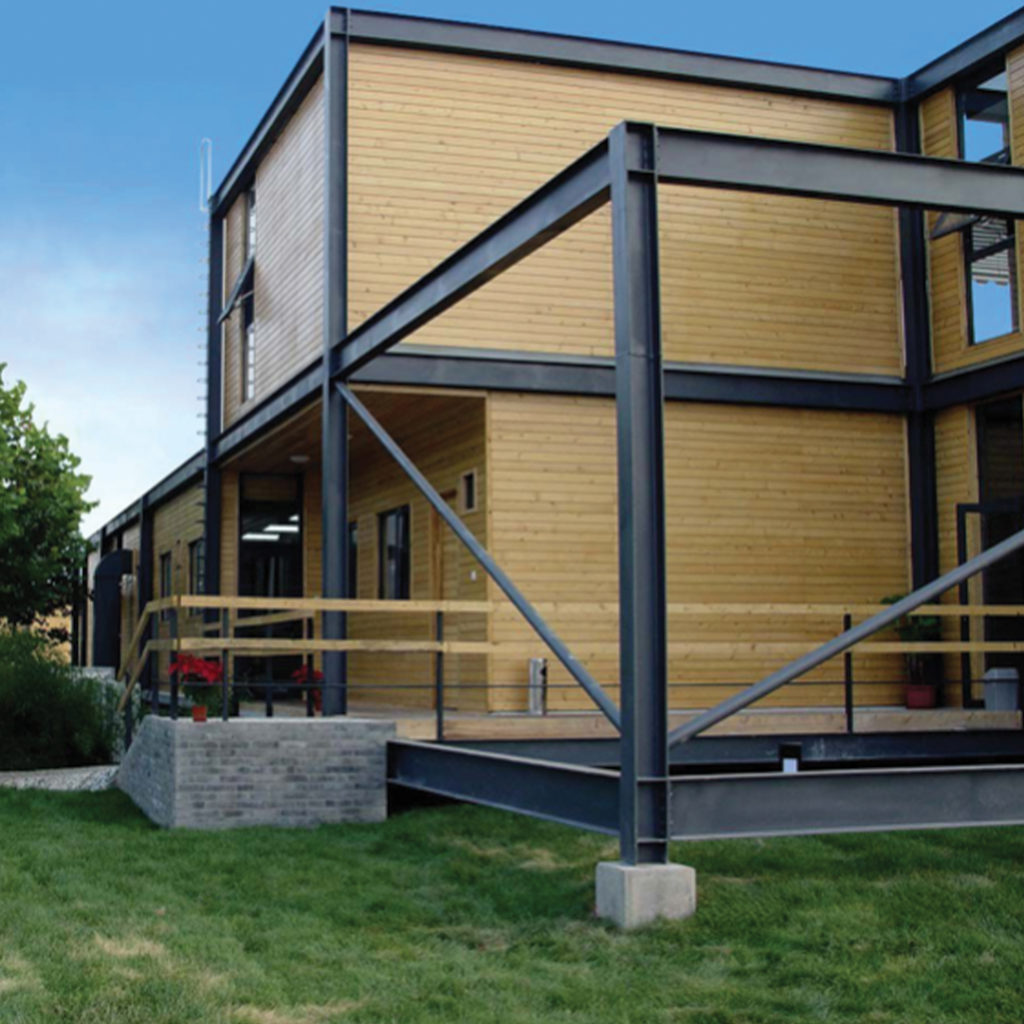
Labor Costs for Framing Per Linear Foot & Square Foot
Most contractors figure commercial rates per linear foot as a part of a total projects cost—expect to pay $5 to $10 per square foot of project or anywhere from $10 to $30 per linear foot. Usually, the larger the project, the lower the unit pricing.
Pairing Installation of a Metal Frame with Drywall
Hanging drywall costs between $1.15 and $2.00 per square foot regardless of the type of stud. Total cost for framing and drywall together runs in the $20 to $30 per linear foot range. Metal frames often seem flimsy but gain exceptional rigidity once a wall covering like drywall or sheathing is attached.
Steel Framed Ceilings for Multi-Story Houses
Steel beams can support more weight over a longer distance than wood perfect for large open concept homes. Framing a ceiling in a multistory home requires additional supports. Expect contractors to utilize structural supports like I-beams, H-beams and Z-beams and heavier gauge steel supports.
Framing Apartments
Installing steel beams costs slightly less than $3,000. Apartments are low-rise or high-rise structure that often utilize structural steel framing with heavy I-beams and heavy load bearing supports. Structural steel allows more variation and options during the design and engineering of the building.
Working with Commercial Structures & Warehouses
Commercial structures run in the $12 to $40 per square foot range with insulation and wall coverings. They employ structural steel supports in combination with light gauge steel studs.
Tiny Homes
DIY metal framing kits are available for tiny homes that run from $13,000 to $21,000 including the trailer foundation and come partially assembled in framing panels. Tiny homes on wheels often use metal to cut down on weight necessary with load restrictions on trailer axles.
The Pollution Solution
Most of the CO2 generated by today’s steel industry comes from the chemical interaction between carbon and iron ore in blast furnaces. This process, known as iron reduction, produces molten iron which is converted to steel. Blast furnace – basic oxygen steelmaking generates about 1500 kg CO2/t of liquid hot metal. As the most widely used reductant, carbon is first converted by the solution loss reaction to carbon monoxide, which is responsible for actual reduction and is thereby oxidized to CO2. A radical reduction in CO2 emissions can be achieved if hydrogen is used for iron ore reduction. Ideally, hydrogen reduction would imply zero CO2 emissions because the resulting off-gas, water, is easily separated by condensation.
The Austrian steelmaker Voestalpine, Siemens of Germany and Austrian renewable energy company Verbund party are building an experimental facility to economically produce hydrogen from water, which would then be used in place of coking coal for steelmaking.
- COST: $750 million spent on direct-reduced steel plant in Corpus Christi, Texas
Volume 203, 1 December 2018, Pages 736-745
Achieving Zero Emissions:
In order to achieve zero emissions in steelmaking, direct reduction of iron ore with hydrogen is being proposed. Hydrogen direct reduction steelmaking requires 3.48 MWh of electricity per ton of liquid steel, mainly for the electrolyser hydrogen production. If renewable electricity is used, the process could achieve zero emissions. The only other possibility is continued use of fossil fuels, but utilize carbon capture and storage (CCS) on the back end.
NOTE: Hazer Group of Australia are already well advanced on the cheap hydrogen required to do this
It is using “cheap as dirt” iron ore to convert methane in natural gas into hydrogen; the carbon content of the gas is captured in the form of high-quality graphite.
As a clean-burning fuel, hydrogen could play a key role in future energy markets, but production methods are still too energy-intensive and costly. Hazer Group (utilizing science from University of Western Australia) has found a way to “halve the cost of hydrogen production”. Its patented process is based on “methane cracking”.
Natural gas passes through a heated iron ore catalyst, breaking down the methane into hydrogen and carbon. This process turns the carbon into solid graphite. Some of the hydrogen is even used to power the system.
If Hazer begins deriving their methane from organic biogas, they could effectively become a carbon sink. “If you look at the whole [carbon] cycle, the carbon that was previously atmospheric CO2 could be stored in the form of sustainable, commercially viable graphite.”(Pocock)
Housing Research
Installing steel studs in the average 2,000 square foot home will run $21,000 with a range of $19,000 to $25,000. Though metal studs currently run in the $2 to $4 per square foot range, steel prices fluctuate over time causing material costs to rise or fall. Regardless of the steel market, labor remains relatively stable at about $5 to $10 per square foot.
Example I: A new 100,000 GSF academic building with a structural steel frame of 15 lbs/sf located in the Mid-Atlantic Region
- Overall cost of building at $350/sf: $350/sf x 100,000 sf = $35M
- Overall quantity of structural steel in the building: $15 lbs/sf x 100,000 sf = 1,500,000 LBS = 750 tons
- Cost of raw steel = $800/tn (ENR)
- Cost of structural steel: $4,000/tn (MGAC benchmark data; note this cost include the $800/tn raw material cost)
- Overall cost of structural steel in the building: 750 tn x $4,000/tn = $3M (9% of total building cost)
Apply 25% tariff to the raw steel portion of the structural steel only:
- Overall cost increase due to tariff: 25% x $800/tn x 750 tn = $150,000 (0.43% of total building cost)
Example II: A new 500,000 GSF high-rise residential building with a structural steel frame of $30LBS/SF located in So Cal
- Overall cost of building at $500/sf: $500/sf x 500,000 sf = $250M
- Overall quantity of structural steel in the building: $30 lbs/sf x 500,000 sf = 15,000,000 lbs = 7,500 ton
- Cost of raw steel = $800/ton (ENR)
- Cost of structural steel: $4,000/ton (MGAC benchmark data; note this cost include the $800/tn raw material cost)
- Overall cost of structural steel in the building: 7,500 ton x $4,000/ton = $30M (12% of total building cost)
Apply 25% tariff to the raw steel portion of the structural steel only:
- Overall cost increase due to tariff = 25% x $800/ton x 7,500 ton = $1.5M (0.6% of total building cost)
Our 4,000-sf house will probably only need 15 lbs / sf X 4000 sf = 60,000 pounds of steel
60,000 lbs = 30 tons @ $800 / ton = $24,000
Structural Steel cost is $4000 / ton X 30 tons = $120,000
TAKEAWAYS
Steel may be too pricey unless we make our own, and mix it with recycled steel as well.
Lumber
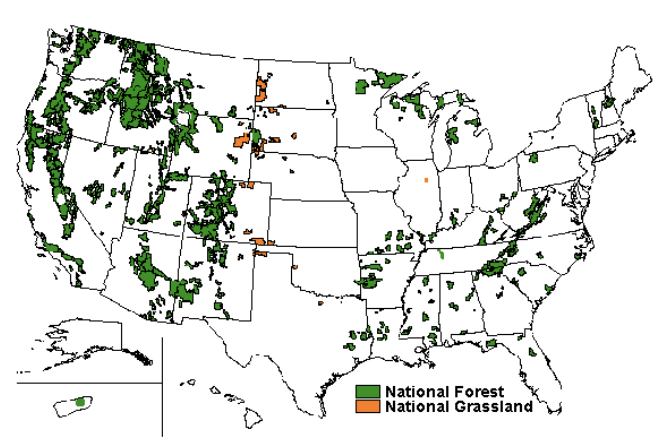
Forests start out as a Carbon Sink, but when they either burn or begin to die, trees
give this Carbon back. Within that window, We could get timber from our Federal Land and turn it into Affordable Housing lumber, and leave a very minimal footprint in the process. To do this, We will need expert people in Our Department of the Interior, as there seems to be conflicting stories about when a tree should be cut down.
It may be best We harvest this timber Ourselves, as there is a lot of Carbon produced through the harvesting and milling and transportation process that We cannot control if We do not do it Ourselves.
However, if We can affordably outfit current sawmills with Carbon-friendly equipment, bring them the timber using electric or hydrogen-fueled transport, then get these sawmills to cut half of what We bring them for free in order to keep the rest for private consumption, We would be happy to talk. These kinds of deals are available to the Private Sector in all of Our endeavors, but We have a very specific agenda, and to get what we need, We are willing to do it Ourselves if necessary. This may not be amenable to some private sector businesses. Let the competition begin. Another positive outcome for these kinds of dealings is to outfit smaller businesses with the tools to do what We need, and let them profit from what is left over.
We would love to help the “little guy” get back out of the shadow Big Business. Whatever works is what We will do.
If We Do It Ourselves: New Lumber Business
$60 Million per Large (Green) Sawmill X 30 Mills = $1.8 Billion
- We also need to Harvest and Transport the wood [80% of the cost of Milling], which raises cost to $3.24 billion.
- $3.24 Billion Loan (will yield $5,568,572,000 in 30 years) $15.47 Million per month payment, or $185.6 Million per year
NOTE: The mortgage payment is covered through the $100 per square foot Building Costs, which will come from Ourselves, as We pay $1.20 per square foot on Our rent. Typically, lumber costs add up to $4 per square foot in the overall building process.
PLAN: Cut down Our own trees and use electric vehicles to bring it to our “zero carbon” sawmills.
Until mills are built, we will utilize private sawmills, bringing them 2X the timber We need for affordable housing, give them X amount to keep for themselves, while they cut the other X amount for free.
Once our Mills are built, and Our projects are finished, We could begin selling wood to Ourselves. This money could go to paying for the Department of the Interior, whose people will already be running and overseeing the cutting down of Our trees, in order that We do it in the most environmentally advantageous, least invasive way possible. If We are indeed forced to build our own sawmills, We could also cut and sell a little extra lumber to Ourselves, in order to help pay back the Loan on the sawmills and harvesting equipment, but only with the blessing of the Department of the Interior.
Large Mills can produce 70 million board feet in a year. (Seneca Sawmills boasts of 650 million board feet capacity at 4 locations, an average of perhaps 162 million BF per sawmill.) The average harvest per acre is 5.5 MBF. A million acres could yield 5,500 MMBF. This means it could take 78 sawmills to process a million cut acres in a year. We do not wish to scare conservationists, but We will need 15 million acres of wood to build all of Our proposed affordable housing, but this is only if we just build it with wood, so firstly, WE ARE NOT GOING TO BUILD ENTIRELY WITH WOOD. Secondly, WE ARE NOT GOING TO CUT DOWN MORE THAN A MILLION ACRES IN A YEAR (if that). We appear to need between 34 and 78 mills of Our own, depending on the capacity. We will start with 30 large well-placed Mills and see if this will suffice.
Housing construction has slowed down since the housing market collapsed in 2009 – this means we will likely not have enough framers and other subcontractors around in order to do all this work, which tells Us We better start training new crews at our Public Schools.
To cut down on wood use, we need steel for structural support, hemp plywood / roofing / flooring, HempCrete for insulation and further support, and ‘clean’ concrete foundations.
BOTTOM LINE: we need green “net zero” floor plans that utilize the best mix of materials for this next century of use.
Apparently, much of the railroads were also shut down as mills closed, so for transport of Our timber, we may be looking at an electric option using the old rail system.
NOTE: The federal government used to to give up 12 billion board feet a year to private companies, although that is now down to 2 billion board feet. We will still be cutting this much down, but only for Our uses. We will not be giving any more of our wood to private companies, unless We feel this is viable environmentally, or because We are getting enough money to pay for something that benefits all of us equally.
TAKEAWAY
In its heyday, the US Forest Service was cutting down about 2-3 million acres of forest a year. Even at this rate, it would take almost 7 years to get all the wood we might need. While this might seem like a sticking point, in truth, The US consumes over 62.5 Billion Board Feet a year, so the wood is out there if We really need it. California alone produced 6 billion BF in the 1980’s, though now the number is 1.7 Billion BF.
DOUBLE-CHECKING THE MATH
We need 1,000 Apartment Buildings in 3,271 Communities, or 3.271 million buildings that average 4,000 square feet. If We build mostly with wood, this translates into 25,000 board feet per 4,000 sf building X 3.27 million buildings or 81,775 million board feet. One million acres of forest holds a potential 5,500 million board feet. This means We would need to cut down almost 15 million acres of forest, which would take 15 years if We behave Ourselves.
BOTTOM LINE: To cut this time in half, We need to build our housing with half the wood. Once again, We need to call upon the Smart People tucked away in their little Construction Silos to step into the light and solve this problem for Us.
Blueprint for a new lumber mill:
- 65% of carbon footprint of wood is from production (sawmill)
- 50% of that happens during the drying stage (dry wood is 50% carbon, captured during photosynthesis)
- The first step in controlling emissions should be to optimize the process so that emissions are minimized. For wood dryers, this can mean lower air temperatures, drying to higher MCs, or, perhaps, completely redesigning the process so a liquid effluent is produced and no gases are released. In addition to optimizing the process, another option is to apply a device to clean the emissions in the exhaust air. Some or all of these options may not be possible or economical in an existing facility or even in a new facility.
- The other 50% is fossil fuel use in sawing and planing of wood (so We need to go electric or hydrogen-fueled in Our equipment)
- Overall message: responsible forestry (selective harvesting, etc) will hopefully make sure wood is overall a carbon capturing avenue
COST:
Seneca spent $60 million on their latest Mill Upgrade. $60 Million X 30 of those Mills = $1.8 Billion. We also need Harvesting and Transportation, that equals 80% of the cost of Milling, which might raise our costs as high as $3.24 billion. A loan this size will generate a mortgage of $15.47 Million per month, or $185.6 Million per year.
NOTE: At $350 per 1000 board feet of lumber, these 30 mills may be producing 2.1 billion board feet or the equivalent of $735 million in lumber on the private market. If we built only with wood, our houses would use 25,000 board feet each. The 2.1 billion board feet we produce a year would be capable of producing 84,000 new houses. If we separate out the cost of land in the equation, the Federal Loan for this many houses is still $33.6 Billion. The wood we use on the houses would normally be $8750 a house, but now it is free, except really, of course, it is not. The good news is that via the loan on the Mills, the wood only costs $2,210 per house built (remember this calculation is for a house completely built with wood, which We won’t be doing) [NOTE: dividing the yearly mortgage payment on the Mills by the 84,000 “all-wood” houses it would produce = $2,210 per house cost)
WORST CASE SCENARIO: If We do not have enough money from renters to pay for all of this, We may have to raise everyone’s rent by $23 a month. ($22 a month X 8 renters per property = $2,210)
NOTES
In 1891, the Forest Reserve Act allowed the president to designate public land reserves. … However, unlike national parks, these forests and grasslands are open to commercial activities like logging, livestock, as well as recreational activities like camping, hunting, and fishing.
We have Bureau of Land Management, Department of Interior, Department of Agriculture, National Forest Service all doing the same job – [NOT ANYMORE] (Read More Forest Fires Timber Logging)
Red Emmerson, billionaire timber man, out bids the competition to go in after a fire, take out all the trees that are burned (90% are supposedly usable), then turns around and sells to Home Depot and the like. These are government lands, and as usual, we subcontract this out, and someone gets rich off the rest of us on our own natural resources. Sheesh.
BOTTOM LINE: This at least proves that we have the trees. Sorry Red, find some other trees. If we keep doing any such dealings in the future, it will be to pay for the Department of the Interior.
A GOOD LOOK AT THE TIMBER BUSINESS IN CALIFORNIA (Click Here To Read PDF Report)
ALASKA EXAMPLE
United States Forest Service (USFS), Alaska Region Office conducts an annual survey of sawmills across the Tongass National Forest – in 2016 they had nine active sawmills, that produced approximately 18 MMBF. They claim this is 16% of the capacity or potential of 113.7 MMBF that could be produced. These 9 sawmills are a mixture of medium and large sawmills.
HISTORY
In the late 1980’s the Forest Service sold about 12 billion board feet per year, providing a steady supply of logs in up and down markets. By the early 90’s that volume dropped to below 2 billion board feet. This put a major strain, to say the least, on mills. US mills went bankrupt and out of business by the hundreds. This devastated communities and caused the entire industry to shift. Out of the 192 million Forest Service acres, 82 million acres are in need of forest restoration. This means the forests need to be actively managed by way of logging, thinning, and deferred maintenance. The by-product of this much-needed work could take medium and long-term pressure off the Softwood Lumber Agreement.
Concrete
Our Affordable Housing will need a lot of Concrete:
- A foundation of 4,000 square feet that would include garages [thickness needs to be at least 8 inches, so will figure 12 inches to include any extra footings or driveway space]
- 4,000 sf X 150 pounds per cubic foot (12” depth) = 600,000 lbs or 300 short tons of concrete
- Goal: build 1,000 such houses X 3,271 different Communities = 3.271 million total houses or 408,875 houses a year for 8 years
- 408,875 X 300 short tons = 122.7 million short tons of concrete per year
These numbers imply we need a business as big as Lafarge-Holcim [US division]. The LafargeHolcim US Cement business comprises 13 cement plants, 97 cement/fly ash terminals, and 2 slag facilities – LafargeHolcim US Aggregate Construction Materials (ACM) business has 98 aggregate sites, 18 docks, 121 Ready-mix sites. Here are its projected 2018 numbers:
- 17 M tons cement (can make between 113 and 170 million tons)
- 89 M tons of aggregate (can make between 118 and 148 million tons)
- 8.8 M cubic meters of ready-mix concrete
- 8,800,000 X 27 (cubic feet in a cubic yard) X 150 lbs = 17.82 million tons
The low-end price of concrete is $4 per sf or $16,000 per housing project. If we build a business as big as Lafarge, we will spend 408,875 (houses) X $16,000 (per house in concrete) = $6.542 Billion
Salary ranges from approximately $31,200 per year for Maintenance Person to $104,304 per year for 7,000 employees. Median would be $67,750 X 7,000 = $474.3 Million in salaries per year. To construct a new dry process cement line producing 1 million tons annually will cost at least $56.5 million
- $56.5 Million US for every million tons produced X 15 (we will need12-18 million tons, so will use a median of 15 million tons) = $847.5 Million
BUT REMEMBER
We need to capture all the carbon dioxide, and if possible, do something useful with it (because trying to stick it underground is going to get old quickly).
Plan
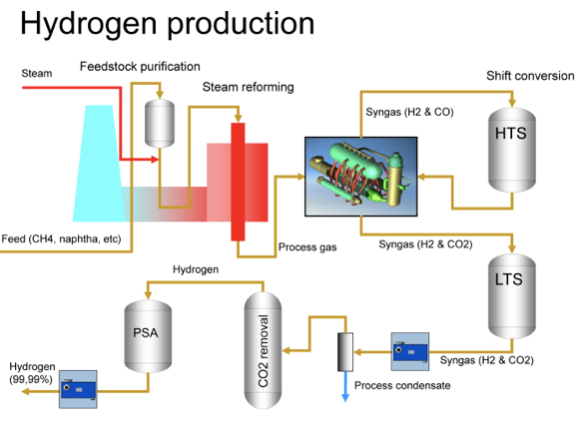
Calera
This company is ready to go. We have lots of leverage we could use to convince industry to get on board; every company out there that emits CO2 into the air is going to incur a heavy carbon tax from us, every year. Perhaps with the capital from one year of this tax, we talk offending companies into installing this carbon capture device and this will allow those companies to continue tax free for a while longer (in the case of oil and coal-fired electrical plants, we hope to eventually take them offline, but that is somewhere down the road right now).
Learn more about Calera on their Bloomberg Profile
Calera will take flue gas and convert it into calcium carbonate powder, basically capturing the CO2 in the process. They will then make us fiber cement siding for our affordable housing. Their product can also help make our driveways and sidewalks and possibly aid in the foundations.
BOTTOM LINE
This solution is a nice starting point, as it looks to cap the carbon coming out of industry right now, and then use it in a meaningful way – some have looked to capture carbon but do not seem to know how to permanently sequester it, let alone actually use it in some meaningful way – as Calera points out, nature has always captured carbon, and used it to form strong calcium carbonate structures like the shells of various marine organisms.
PRICE TAG: Supposedly the LEILAC / Calera technology cost $23.6 Million
CHEMISTRY QUESTION
- If: CO2 + Ca(OH)2 [Calcium hydroxide, or slaked lime) leads to CaCO3 (calcium carbonate) + H2O
- And: CO2 + 2NaOH + CaCl2 leads to CaCO3 + 2NaCl + H2O
- How can we get: CaCO3 + H2 (pure hydrogen for our fuel)?
Hazer in Australia takes CH4 (methane) and turns it into 2H2 + C (graphite) using Iron-ore as a catalyst.
We have lots of methane coming out of many holes. We just need to capture it. If We don’t flare it off at Oil Wells but capture it, We could use it. If instead of wasting billions of gallons of precious water cleaning cow dung out of factory farm feed lots and into Our groundwater, We could use it. We could even get methane out of our own poop.
We want the end product to be: 2H2 + C + CaCO3 – Could CH4 + CO2 + CaO [Calcium oxide, or quicklime / burnt lime] lead to 2H2 + C + CaCO3?
WHERE’S A CHEMIST WHEN YOU NEED ONE?
Probably any presence of Oxygen in the equation, and that damn Hydrogen will bully the Calcium oxide and the Carbon Dioxide and take the Oxygen away from them to make water.
BOTTOM LINE
If those Chemists wanna make the big bucks, they need to both capture and utilize carbon dioxide and methane and even carbon monoxide, preferably mimicking some process in nature versus Frankenstein-ing the thing, which has historically always come back to terrorize the countryside.
Other Cement Ideas In the Running:
Fly ash cement
- Alkali activated and “geopolymer” cements gain their strength from chemical reactions between a source of alkali (soluble base activator) and aluminate-rich materials. The source of the aluminate-rich materials will be an otherwise waste product – fly ash, municipal solid waste incinerator ash (MSWIA), metakaolin, blast furnace slag, steel slag or other slags, or other alumina-rich materials. They tend to have lower embodied energy/carbon footprints than Portland cements (up to 80-90 per cent, but this is dependent on the source of the aluminate-rich material). Production is now covered by a standard: PAS 8820:2016 Construction materials.
- TAKEAWAY: This method is getting a lot of press. Perhaps our New Steel Plants can produce some of the needed materials.
Ferrock
- Created by David Stone, it is composed partly of iron dust reclaimed from steel mills and currently sent to landfill. Stone has patented the name Ferrock and formed a company, IronKast, which is in the early stages of commercializing the patent with pilot implementations in marine environments being tested and benchmarked by the University of Arizona.
- It emits no carbon dioxide during production and, in order to cure it, as with Portland cement, carbon dioxide is required as a catalyst thereby making it carbon negative.
- When CO2 dissolves into water it forms carbonic acid. If iron dust is present it combines with carbonate molecules and precipitates back out of solution as solid iron carbonate. The resultant material has a greater compressive strength than mortar made with Portland cement. However, because of the limited availability of the iron dust, it will never completely replace all uses of Portland cement.
- TAKEAWAY: Can we make David Stone an offer he cannot refuse? Perhaps we need to make this guy some iron dust.
Note 1: Water-to-solids ratio (w/s) of 0.24, with a range of 0.18 to 0.30, serving mainly as an agent of mass-transfer and does not chemically participate in the reaction.
Note 2: Fully cured samples contain between 8% and 11% of captured CO2 by weight [8, 9]
Besides its unique chemical properties as a carbon sink that emits valuable hydrogen gas as a byproduct, Ferrock additionally presents technical characteristics that have potential to make it a promising substitute for cement. Ferrock has similar functional properties in terms of its fresh-state behavior and workability. In addition, the iron-based binder requires a fractional amount of time to cure compared to OPC; 4 days of carbonation compared to the 28 days of hydration that is required for cement to cure. The curing process for Ferrock also has the theoretical potential to be further expedited based on the purity of the compressed carbon dioxide.
Hempcrete
- Another substitute for concrete is Hempcrete, which is made from hemp and lime. Hemp, when growing, absorbs atmospheric carbon dioxide. Lime, when applied this way, also absorbs atmospheric carbon dioxide, making the material carbon negative.
- While not having the structural strength of concrete (its typical compressive strength is around 1MPa, over 20 times lower than low grade concrete and its density is 15 per cent that of traditional concrete), with a k-value of between 0.12 and 0.13 W/mK, it offers some insulation value. It can be used in many situations where concrete is currently used. It is of interest also because of its breathability, which lends it to use with other national building materials to create buildings that have a pleasant internal atmosphere that does not suffer from damp or condensation.
- TAKEAWAY: It appears we still need something stronger than this for the foundation, but at least it can substitute for many of the other places where cement currently is used.
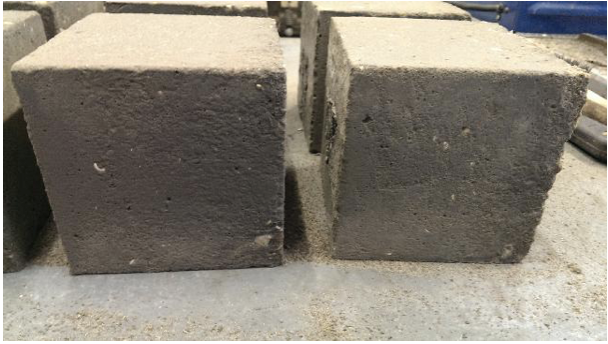
Back To Direct Separation:
- The LEILAC (Low Emissions Intensity Lime And Cement) project is trialling a new type of carbon capture technology called Direct Separation. To this end it is about to build and operate a pilot plant at the HeidelbergCement plant in Lixhe, Belgium.
- The LEILAC project is based on a technology called Direct Separation, which aims to enable the efficient capture of the unavoidable process emissions from lime and cement production.
- Calix’s technology re-engineers the existing process flows of a traditional calciner, indirectly heating the limestone via a special steel vessel. This unique system enables pure CO2 to be captured as it is released from the limestone, as the furnace exhaust gases are kept separate. It is also a solution which requires no additional chemicals or processes, and requires minimal changes to the conventional processes for cement as it simply replaces the calciner.
- As two-thirds of CO2 emission from cement production is generated from the limestone itself, this technology offers a unique opportunity as it can capture these emissions without significant energy or capital penalty. The energy losses associated with Direct Separation technology are primarily heat losses in the equipment, and CO2 compression (for transport and storage).
- It also enables the use of carbon capture techniques, which have already been already developed by the power sector to be applied to the heating emissions.
- This innovation requires minimal changes to the conventional processes for cement, replacing the calciner in the Preheater-Calciner Tower. For lime there is no product contamination from the combustion gas. The technology has the potential to be used with alternative fuels and other capture technologies to reach the targeted 80% emission reduction in 2050.
Making Greener Cement
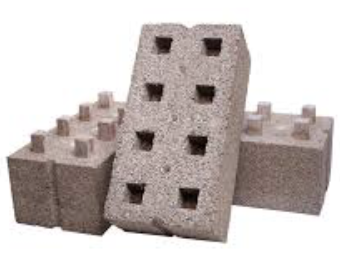
The direct emissions of cement occur through a chemical process called calcination. Calcination occurs when limestone, which is made of calcium carbonate, is heated, breaking down into calcium oxide and CO2. This process accounts for ~50 percent of all emissions from cement production.
Concrete is essentially sand and gravel held together with cement. To make cement, limestone is baked at high temperatures in huge furnaces. The process releases carbon dioxide in two ways: From the burning of fossil fuels as well as the chemical conversion of limestone to lime.
Most concretes used are lime-based concretes made from calcium silicate, such as Portland cement. The main ingredient is limestone or calcium carbonate (CaCO3). Portland cement is made by heating the raw materials including the limestone firstly to above 600°C and then to around 1450°C to sinter the materials. This emits carbon dioxide and produces calcium silicate ((CaO)3·SiO2). When it is turned into liquid cement with the addition of water and exposed to the air it absorbs carbon dioxide again, to reform into calcium carbonate (CaCO3), and hardens.
- Heat Recovery and Efficiency – The high temperatures associated with cement production can also be used to generate steam that is then used in steam turbines.
- Green Concrete – Materials substitution, for example the addition of wastes and geo-polymers to clinker, can reduce CO2 emissions from cement manufacture and save energy. Clinker may be blended with alternative materials like blast furnace slag, fly ash from coal fired power plants and natural pozzolans. Use of granulated slag in Portland cement may increase energy use in the steel industry, but can reduce both energy consumption and CO2 emissions during cement production by about 40 per cent.
- This EnergyStar guide for energy and plant managers – Energy efficiency improvement and cost saving opportunities for cement making, outlines over 50 specific energy efficiency opportunities for all stages of the different production processes of different types of cement. This includes over fifty changes to production methods such as: using high-efficiency roller mills, energy management and process controls, kiln shell heat loss reduction, use of waste fuels, conversion to pre-heating for the kiln, pre-calciner kilns, better maintenance and optimization of parts and systems, oxygen enrichment, high efficiency motors and variable speed drives, using steel slag in kiln and much more.
Alternatives to Portland cement
- “Limestone-free cements can be achieved through chemical ‘activation’ of by-product materials or by producing an array of cementitious compounds based on magnesium oxide,” according to Jenny Burridge, the head of structural engineering at The Concrete Centre, UK. Here are the main ones:
Magnesium silicates
- This involves the accelerated carbonation of magnesium silicates instead of calcium carbonates under high temperature and pressure, with the resulting carbonates then heated at low temperatures to produce magnesium oxide, with the CO2 generated being recycled back in the process.The use of magnesium silicates eliminates the CO2 emissions from raw materials processing. In addition, the low temperatures required allow the use of fuels with low energy content or carbon intensity (biomass), thus potentially further reducing carbon emissions. As with Portland cement, production of the carbonates absorbs carbon dioxide by carbonating part of the manufactured magnesium oxide using atmospheric/ industrial CO2.
- NOTE: Novacem (a spin-out company from Imperial College London) tried making cement using this method [claimed to absorb up to 100kg more CO2 than it emits, making it a carbon-negative product, which could revolutionize the industry] They had problems trying to scale up production and the company became insolvent in 2013.
Calera
- Calera’s process involves the capture of raw flue CO2 gas from industrial sources and converting it into calcium carbonate cement-based building materials. By converting the gas into a solid form of calcium carbonate it permanently sequesters the CO2.
- Commercial demonstrations have included the capture of flue gas from power plants and burning coal, without concentrating the CO2. The flue gas is contacted in a scrubber with an aqueous alkaline solution that effectively removes the CO2 and a calcium source that results in the formation of the special calcium carbonate product that is then dried to a free flowing powder.
- It requires sources both of alkalinity and calcium. Some industrial waste streams contain both, like calcium hydroxide (Ca(OH)2). Another option is separate streams, one for alkalinity, such as sodium hydroxide (NaOH), and one for calcium, like calcium chloride, which can be naturally occurring or found in the waste streams of existing chemical processes.
- NOTE: would have to work with private industry, who would take a shit and charge you for it if they see the demand. Perhaps we can tax all waste streams to incentive them to capture it and give it to us, or pay for the apparatus for everyone and thereby take what we want for free.
- The earth’s atmosphere has had higher concentrations of CO2 in the past and nature dealt with these high levels of CO2 by a mineralization process whereby marine organisms use CO2 to form calcium carbonate structures that deposit on the ocean floor over time. It is estimated that up to 100 million billion tonnes of CO2 is stored in the geological record in the form of calcium carbonate. Calera’s process for CO2 reduction involves the capture of CO2 gas from industrial emitting sources and converting the CO2 into a novel calcium carbonate cement system.
- CHEMISTRY: CO2 + Alkalinity + Calcium = Calcium Carbonates (alkalinity and calcium can be all in one substance, like calcium hydroxide [Ca(OH)2], or in two different streams like a caustic soda [2NaOH] and calcium chloride [CaCl2].
- It can function as a supplementary cementitous material (SCM) in traditional concrete mixes where the environmentally sustainable calcium carbonate can replace a portion of portland cement, helping reduce the overall carbon footprint of traditional concrete. The Calera calcium carbonate can also be used as the sole cement or binder system in concrete products. Calera developed wallboard and cement board products where the unique binder can be used instead of gypsum, magnesium oxide, calcium silicate or portland cement.
- Calera Calcium Carbonate was used as a supplementary cementitous material in several projects including sidewalks in a local municipality and flatwork in a commercial office building where it replaced approximately 15% of portland cement in the concrete mixture.
- The unique calcium carbonate cement made in the Calera process can be used without any other cement or binder system to make concrete products. Calera demonstrated the ability to make a variety of decorative concrete products such as countertops, plant holders and benches. The products contain traditional sand and aggregate all held together in a concrete mix by the calcium carbonate cement. Calera also produced full fiber cement board sheets on a commercial line, exceeding strength requirements with formulations that are lighter weight than many existing cement board products.
- The result is a high strength material that can be used without any other cement or binder system to make concrete products from countertops, plant holders and benches to fibre cement board sheets on a commercial line, exceeding strength requirements but of a lighter weight than many existing cement board products.
SOLIDIA
- SOLIDIA cement is a related product and process that cures concrete with carbon dioxide, say, from flue gases, and is currently at commercialization stage. It requires less limestone as a result and can therefore be fired at lower kiln temperatures. It requires less energy and generates around 30 per cent less greenhouse gases than ordinary Portland cement.
- NOTE: Nice effort, but we should reach higher than 30%.
Celitement
- Celitement is a cement substitute produced at temperatures below 300°C under a process developed by the German Karlsruhe Institute of Technology KIT. It will therefore require less energy and emit fewer greenhouse gases.
- Celitement is calcium hydrosilicate, a raw material already containing calcium (CaO) and silicon (SiO2), though in the wrong ratio. It must be processed using an autoclave under saturated steam conditions, grinding and the addition of water. All of this emits around 50 per cent less carbon dioxide than Portland Cement. But it is still at the R&D stage.
- NOTE: Is 50% the best we can do? If we try for better, it appears we may need to allocate some $$ to R & D to get it right. Tick Tock.
Aether
- Aether is a partnership by Lafarge, a world leader in building materials, with two technical centers, BRE (UK) and the Institute of Ceramics and Building Materials (Poland). Technically, this is a Belite-Calcium Sulfo-Aluminate-Ferrite compound. Trials found that Aether generates 20 to 30 per cent less CO2 per ton of cement than pure Portland cement (CEM (I) type) and had a compressive strength similar to Portland cement. There is a European standard now underway. This is still at the R&D stage; the key problem is that it hydrates slowly.
Plastic
PLASTIC STRATEGY IS THREE-FOLD
1 – We have to collect and get rid of the old plastic we have made
- Burn it (will need to cap that toxic residue if we do)
- Make roads out of it (10% of the asphalt mix)
- Make plastic bricks for housing out of it (Our kids could build shelters in developing countries / around outskirts of Our Global Schools)
- Can also work as a binder in concrete pavement – best mix seems to be 84% Bituminous + 6% Plastic + 10% Rubber
2 – Tax the hell out of plastic use currently, until we outlaw it completely, [this will fund R & D and Our resulting New Plastic Business]
- 10 cents per plastic bag ($10 Billion could be collected)
- 10 cents per plastic water bottle ($5 Billion could be collected)
- 10 cents for every straw ($15 Billion could be collected)
- 10 cents for every Paper Bag
- 10 cents for coffee or other drink cups
- 10 cents for any other single use item that We decide can or should be taxed (pizza boxes, fast food containers, grocery store cans, bottles, wrappers, etc.)
3 – Introduce our New Plastic Business
- We talk to Our scientists – they are reasonable people – they do crazy stuff like sell penicillin to everyone for $1. We go into business with them, hand them a few suitcases full of cash to continue their research, and get the formula and logistics for making infinitely recyclable plastic. Eugene Chen at Colorado State University has already figured it out, but no one in the private sector wants any part of it—it’s not cheap enough for them (the private sector likes cheap).
- We create a business around this new plastic. We render custom-made boxes to spec for Amazon, Apple, basically everyone who is anyone.
- When you order something, there is only one choice for shipping: Our $12 box. The box costs you $10, and Amazon gets a dollar (payola), and Our company gets a dollar (the cost of melting down and reproducing the boxes)
- Upon getting your shipment, you drop your plastic box into One of Our Neighborhood Bins (or at your local school), and you get a “credit” for returning it, which lets all vendors know that you have a “credit” coming for a new plastic box [of any size) whenever you need it, already paid for. That way, the next time you order something, there will only be a $2 charge for shipping materials only. ($1 for the Vendor, $1 for Our company).
- If you throw your box in the street, your next purchase will incur another $12 charge. Not smart. Or maybe you are a business needing lots of things shipped to you, so perhaps you have 20 boxes in play out there in this digital box universe. All boxes cost the same thing, all of them are interchangeable.
- ProtoCycler [https://redetec.com] can take recycled plastic, make it into 3-D printer ready spools – so now our kids can take truly recyclable plastic and help us fund education by perhaps running this whole plastic business.
Other businesses in recycling:
- Integrate with Our Rail / Hyperloop shipping business and local driverless Pod Delivery Postal Service
- Have Schools make cloth bags in “Textile Class”, as well as organic packaging materials (seehttps://ecovativedesign.com]*, in an attempt to cover all needed forms of packaging (glass is ok with no labels or coloring, too)
- Coffee Cup Business – fashioned in the same way as Our Recyclable Plastic Business, you will get a “credit” for returning the cup anywhere, which will show up in your account when you get your next cup of coffee. Seems these ideas are already floating around. Go here for some details.
*Biodegradable food packaging grown from mushrooms…
Recyclable Plastics Businesses
General Facts:
- Americans used about 50 billion plastic water bottles last year. However, the U.S.’s recycling rate for plastic is only 23 percent, which means 38 billion water bottles – more than $1 billion worth of plastic – are wasted each year
- The average American throws away approximately 185 pounds of plastic per year.
- Americans use 100 billion plastic bags a year, which require 12 million barrels of oil to manufacture. It only takes about 14 plastic bags for the equivalent of the gas required to drive one mile.
- Americans use 500 million plastic straws every day. That would be about 182.5 billion straws a year. A plastic straw weighs about 0.4 g. Do the math and you’ll arrive at about 73,000 metrics tons of plastic straws per year.
- 14 plastic bags have enough oil in them to fuel your car for one mile.
TAKEAWAYS
We need to close the loop on the number of containers We produce, and just keep recycling and reusing them. (Think of our money, for example: nobody seems to think it is a good idea to just print enough cash for everyone, so we have to share it – it gets “recycled” around and reused, then decommissioned and replaced when it gets too old). We need our systems to keep reusing the same material over and over. Biodegradable offerings would only be acceptable in small quantities, and only if it helped revitalize or return nutrients to the soil in the process, or would somehow degrade into a product We could also use (example: burning hydrogen fuel leaves water as the byproduct).
Waste Management Businesses
Waste Management has many facets to it:
- Turning human or animal or food [organic] Waste into Energy, Fertilizer, and usable Water
- Collecting and Reusing packaging Waste, or Recycling it so it can be reused
- Discontinuing any Waste products that cannot be recycled or reused easily, then take what has already been made and find the best places to usefully store it in asphalt, concrete, housing, 3-D printing spools, etc.
- landfills should no longer be an option, though gases from old landfills can be captured and used as a fuel source
OVERALL GOALS
- We will offer the most user-friendly ways to minimize waste creation, and maximize waste collection and repurposing / utilization.
- By limiting choices for packaging materials, offering an easy collection strategy, we will make Waste Management cost effective.
- We will take human sewage and food waste and turn it into Hydrogen first, so it leaves a footprint of clean water.
- Many companies have started producing Waterless toilets that take solid waste and turn it into fuel, fertilizer, even usable water. Ghana and Kenya are two recent recipients of this innovation.
- Freshwater Pollution Costs US At Least $4.3 Billion A Year ($2.9 billion from recreating in polluted water) Industry causes the other $2.3 Billion. This may need to be collected through fines.
Bottom Line:
Sorry Kids. You will be making these in one of your Global School Projects, and We will be giving them to your country of choice, unless it gets used by Our Homeless or Off-the-Grid People, or if FEMA needs them in the Tiny Mobile Homes We are also going to build toilets that turn poo into power.
In Transportation
BATTERY-POWERED VEHICLES
We hope to go into the new Pod Car Business in order to produce at least 6,000 vehicles X 3,271 Communities for their ride-sharing program. That is 19.6 million 50 KwH Batteries needed to power these Cars.
Oak Ridge National Laboratories [who will be on Our Federal payroll] has an aluminum-ion battery that may replace Lithium-ion technology.
NOTE:
We are making graphite through Our Waste Management [methane to energy] business, which We hope to use in producing these new Batteries (See Hydrogen Fuel Manufacture).
HYDROGEN-POWERED VEHICLES
Hydrogen is the most abundant element in the universe, and energy is created when it combines with oxygen to make water as a clean by product. Unfortunately, We need it in liquid form in order to store it, and it is not cheap to convert it to a liquid, and once We have it there, it is not easy to keep it in liquid form, either. Science has been perfecting this for 150 years, however, and it is getting easier all the time. We can do this.
In Fukuoka, Japan, the automaker is converting human waste into hydrogen. The process is pretty simple. At a wastewater treatment plant, like the Fukuoka City Central Water Processing Plant, sewage is separated into liquid and solid waste. The solid waste, called sewage sludge, is usually thrown into landfills. But in Fukuoka, microorganisms are added to the mix. These microorganisms break down the solid waste, creating biogas, about 60% methane and 40% carbon dioxide. Then, workers filter out the CO₂ and add water vapor, which creates hydrogen and more CO₂. They extract the CO₂ again, and voila: pure hydrogen.
Sources for Hydrogen Production are plentiful, and if We can make it more affordable to create, Hydrogen Fuel can have many uses. It is a good fit for Our Heavy Freight Shipping Business, to power the Rail Transport. At airports, Hydrogen fuels many of the vehicles, including tugs, forklifts, and all the heavy duty and passenger vehicles.
Soon electric batteries will become lighter and more powerful. For now, however, it appears that hydrogen may have a niche when having to power the heavier machinery: vehicles like trains or buses that carry a lot of weight for great distances. It may even be true that while domestic airline flights can be charged with battery power, large planes on longer international flights may need a boost from hydrogen.
Bottom line: The Sun is made of mostly hydrogen, so whoever put the Sun there felt like that was the best stuff to do the job of sustaining life. Solar power would not exist without hydrogen first. The patent on Hydrogen Power has got to have run out by now; perhaps We should jump on this.
SMART ROADS
By adding Sensors directly into the roads, the movement of cars can capture electricity (the Piezoelectric effect). It might be smart to add GPS to the roads also, so that our new transportation grid could operate under any conditions.
Other Notes
- We can reuse asphalt and concrete [grind it up].
- It is better to collect rain before it hits the ground, would our 2nd Tier collect rain, too?
- For every block of Community street We close down, We will need to provide at least 66 parking spaces somewhere on the perimeter.
- Supposedly Uber operators can drive 30 different people around in a 12-hour day [X 3000 cars gets 90,000 people a ride in a 100,000 population] [My calculation is 6% or 6000 cars to service 100,000 people].
OTHER THINGS TO BUILD
- Pod Car Magnetic Levitation Rail (a la SkyTran) supposedly cost $13 Million a mile (roads are $25 million a lane / mile, Rail is $35 Million / mile)
- Roundabouts at intersections that are not super-congested are recommended by smart people.
For other interesting Urban Transit Designs
On Rails
Functional Classification of US Roads
The U.S. ‘Interstate System’ — the highest classification of arterial roads and streets—provides the highest level of mobility, at the highest speed, for a long uninterrupted distance. [46,334 Miles (1.2% of total distance), gets 23.9% of total usage]. This is where Maglev or even Hyperloop Technology could be used, and possibly heavy rail transport needed along some routes.
Air quality would improve if people utilized ground travel over air travel. Also, these high-speed rails could handle freight, and get these heavier vehicles off our main roads, where they cause significant damage over time.
On Runways
ELECTRIC AIRLINES
We need to get electrical aircraft propulsion off the ground. Perhaps with continued breakthroughs in battery storage, We can create longer-lasting and lighter versions, but until then Our airplanes may have to remain domestic in their flight range capabilities. (Hydrogen fuel is an option as well, of course).
Our first priority is getting Our own Federal Government people around more cheaply. Our Second priority is to get our Global School students around more cheaply. To do this, We will fill our planes with 75% civilians paying the best price We can offer them. Meanwhile, we will make the friendly skies more Carbon Friendly as well.
Notes
Aircraft manufacturers (like Boeing) are more profitable than either Airlines or Airports, who earn lower returns on invested capital. Meanwhile, Airlines who purchase these aircrafts incur the most risk, as earnings are more unpredictable.
Conclusion
We must both compete against Aircraft manufacturers to drive down their exorbitant profiteering, plus charge them something for helping create the airport infrastructure, without which their industry would not exist. Buckle up Boeing. It’s your turn to get taken for a ride.
Reality
We will not go to bed with some sleazy Start-up just to make Boeing jealous for cheating on Us all these years. We will keep the skies friendly, but We are going to see other people. Non-smokers are preferred. Quiet. And Someone who definitely pay their own way.
Running the Numbers, Just in Case…
750 planes (equivalent to Southwest Airlines fleet) @ $30 Million per plane = $22.5 Billion Loan